En la amplia mayoría de sistemas de producción industrial, un alto porcentaje de la carga de trabajo es realizada de forma automatizada mediante equipos industriales. Dichos equipos tienen un funcionamiento mecánico que repite el proceso de forma automática, si bien requiere de una supervisión que permita solventar posibles paradas imprevistas, así como su activación para escenarios posteriores.
Sin embargo, esta situación no hace que un sistema de dichas características esté exento de errores y variabilidad en su producción por diversos motivos. Es por ello que resulta de especial interés tener un conocimiento detallado de cuál es el estado actual de cada uno de los equipos respecto a su capacidad y eficiencia productivas. Para ello, se pueden aplicar diferentes enfoques que permitan cuantificar la calidad del funcionamiento, basándose en información recogida y almacenada de dichos procesos, la cual permita su análisis para extraer información de interés.
- El primer enfoque radica en el estudio de los tiempos de producción de los diferentes artículos o productos en cada uno de los equipos disponibles en el sistema. Dada la información previa almacenada acerca de dichos procesos productivos, es posible generar informes individualizados para cada producto y/o equipo que indiquen los tiempos de producción asociados a éstos, así como las posibles desviaciones entre diferentes procesos históricos registrados.
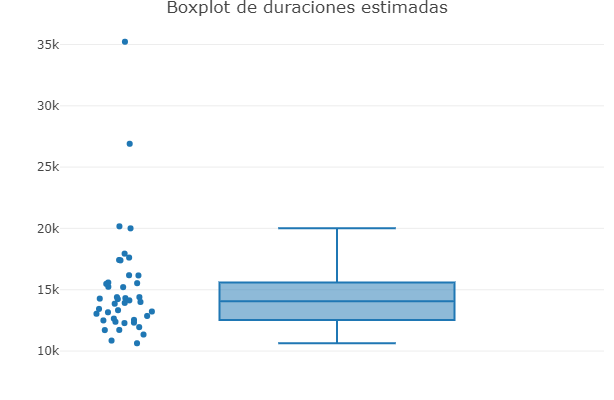
Figura 1 – Boxplot generado con los tiempos de producción históricos de un producto.
- Por otro lado, existen posibles paradas de los equipos por diferentes motivos (fallos, falta de material, etc.). Dichas paradas, en caso de ser registradas en una base de datos según suceden, deberán ser tratadas y agregadas para obtener información útil para la empresa, tanto a través de la distribución de dichas paradas a lo largo del proceso según su tipología, así como mediante los tiempos de parada y útiles asociados. De este modo, será posible identificar si dicho equipo se encuentra en parada durante un tiempo mayor del esperado, así como las causas principales de dichas paradas, lo cual permita abordarlas y evitarlas en procesos posteriores.
- Por último, existe un coeficiente dentro del ámbito de la eficiencia industrial, conocido bajo las siglas OEE, provenientes del término en inglés Overall Equiment Effectiveness, y traducido habitualmente como Efectividad Total de los Equipos.
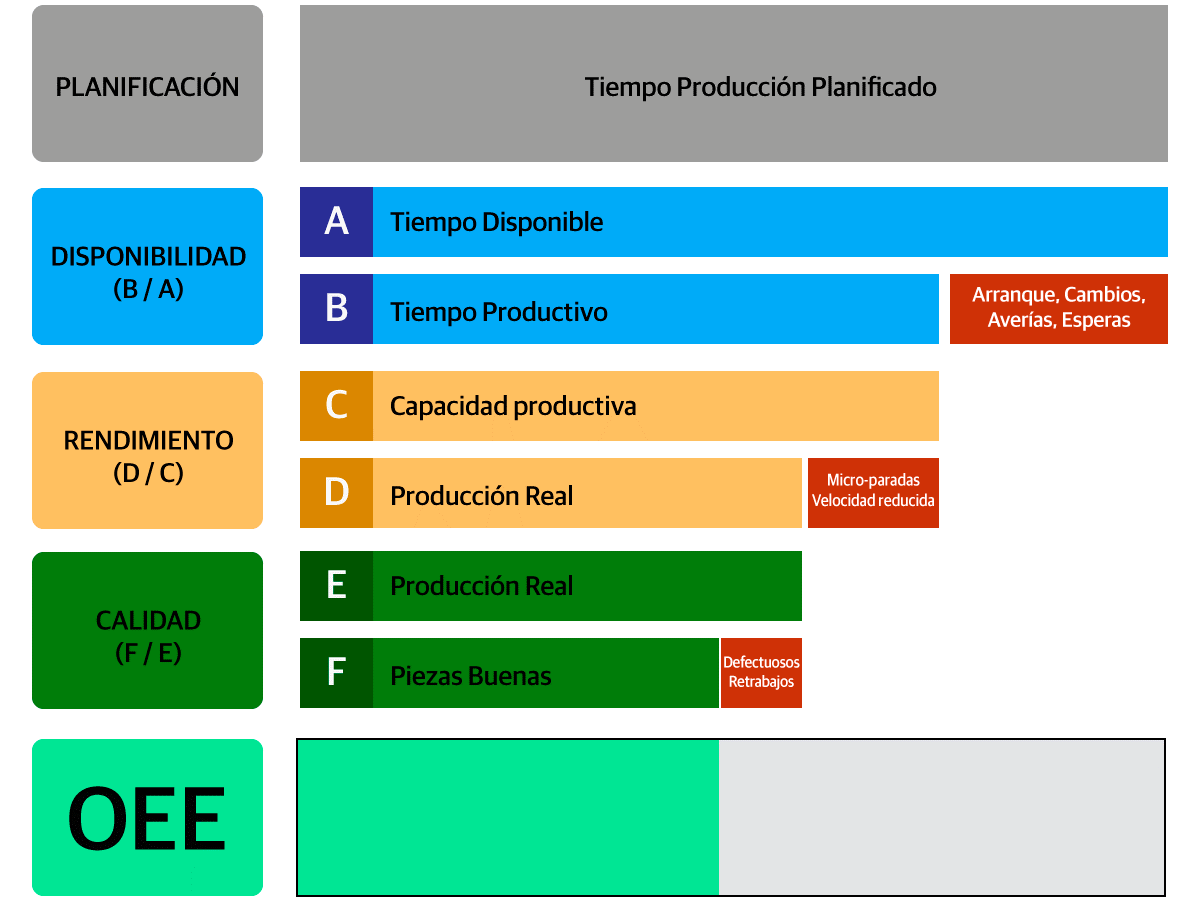
Figura 2 – Esquema de cálculo del coeficiente OEE.
Dicho coeficiente será generado a partir del producto otros sub-coeficientes, tal y como se indica en la Figura 2: disponibilidad, rendimiento y calidad. La disponibilidad se obtendrá como la proporción de tiempo productivo del tiempo total disponible (obviando paradas como las previamente indicadas). El rendimiento viene dado por el cociente entre la producción real y la capacidad productiva del equipo analizado. Finalmente, la calidad representa el porcentaje de piezas buenas obtenidas a partir de la producción total generada. Estos tres coeficientes toman valores entre 0 y 1, por lo que al calcularse el coeficiente OEE como el producto de éstos, implica que, del mismo modo, variará dentro de ese mismo rango. Así, a mayor valor de OEE, mejor eficiencia del equipo en estudio.
Todo esto muestra la importancia de la recogida automática de datos en sistemas productivos industriales, lo cual permite obtener información de gran utilidad para la empresa, tanto para conocer el comportamiento habitual de los equipos en la producción de cada posible producto, para identificar las causas de retrasos en la producción, o para evaluar la efectividad productiva de cada uno de los equipos.
Data4Value